Heating begins at Hanford radioactive waste treatment plant
.jpg)
The heaters are at the heart of the Waste Treatment and Immobilisation Plant (WTP) which is being designed, built and commissioned by Bechtel for the US Department of Energy. When complete, the plant - described as the largest radioactive waste treatment plant in the world - will process and stabilise much of the 56 million gallons (212,000 cubic metres) of radioactive and chemical waste from Hanford's 40 years of operations producing plutonium for US defence purposes. Vitrifying the waste converts it to a glass form which is stable and impervious to the environment.
The melters - each measuring about 20 feet by 30 feet (6 metres by 9 metres) and 16 feet high are part of the WTP's Low-Activity Waste facility.
The comprehensive process for heating up the first melter will ensure the temperature increases slowly and insulation inside the melter dries out slowly. Temporary startup heaters have been inserted into the top of the melter, and glass beads, called frit, will be added. As the beads melt and a molten glass pool rises to cover electrodes inside the melter, the melter’s permanent heating equipment will take over to maintain the operational temperature. The Hanford team has released a 3D animation illustrating the process.
"When we finish heating up the first melter, that will be another significant step in commissioning the Waste Treatment and Immobilisation Plant for future operations,” said Project Director and Bechtel National Inc Senior Vice President Valerie McCain.
After heatup, the first melter will remain active using nonradioactive materials, while lessons learned from the first melter will be implemented in the programme to heat up and commission the second melter. When both melters are at operating temperature, the facility will run simulated waste through them as they continue preparations to vitrify waste.
_17992.jpg)
_75800.jpg)
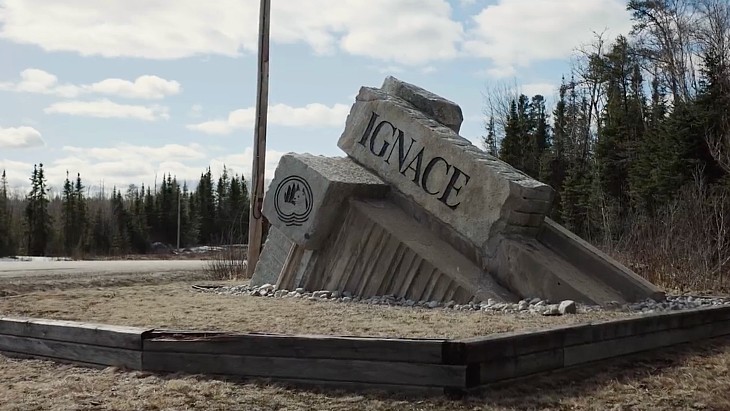
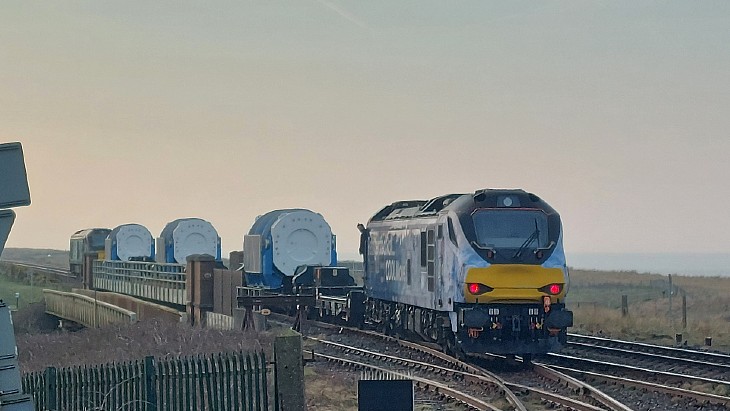
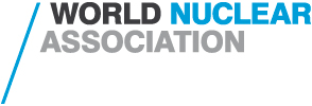